Engineered for Excellence: U.S.-Made Steel Conduit Sets the Standard for Safety and Performance
For experienced electricians and electrical contractors, it may not take long to realize they’re working with substandard conduit. Instinctively, they’ll know that making connections is harder than it should be—or that it’s challenging to bend the tubing or feed cable through the conduit.
Why does this matter? For one, poorly built materials can slow down a job because it usually requires more effort and finesse to complete an installation, according to Greg Maurer, Director of Technical Services and Quality Assurance at Wheatland Tube and Western Tube, part of the Zekelman family of companies.
What’s more: Conduit that doesn’t meet industry specifications increases safety risks and compromises performance, either immediately or by introducing long-term vulnerabilities that can dramatically shorten the lifespan and efficacy of a project, he says.
An overly thick weld bead, for example, could damage the electrical wire as it’s pulled through, creating issues immediately.
“If that weld bead isn’t controlled properly and it’s too high or too sharp, you can damage the wire and cable that’s inside, and those problems could lead to a short or a fault or something potentially worse,” says Maurer.
The Standard of Quality
Western and Wheatland Tube produce a variety of electrical products, including conduit, EC&N (elbows, couplings, and nipples), ZI-Strut, and a full line of accessories. Maurer’s team keeps an eye on the North American marketplace to ensure that steel conduit products sold in the U.S. and Canada, from all manufacturers, comply with domestic regulatory standards.
There are several sets of standards that apply to electricians and electrical contractors, including those adopted by organizations such as the American National Standards Institute (ANSI), the Canadian Standards Association (CSA), and the United States-based National Fire Protection Association (NFPA).
The key certifying organization for the industry in the U.S. and Canada is Northbrook, Illinois-based UL Solutions, whose standards mirror those of the U.S. National Electrical Code. UL standards dictate elements of manufacturing ranging from product dimension to wall thickness, mechanical property requirements, and requirements for coating metal conduit. Different UL standards pertain to different types of conduit: UL 797 governs electrical metallic tubing (EMT), while UL 1242 addresses intermediate metal conduit (IMC), and UL 6 covers rigid steel conduit (RMC).
A UL stamp on a piece of conduit indicates that the product meets UL regulatory requirements. Companies offering UL-certified products are also subject to regular, on-site field audits by third-party inspectors to ensure ongoing compliance. Zekelman’s North American factories are audited at least quarterly, Maurer says.
Still, it’s not practical for an independent auditor to check every single piece of conduit before it’s shipped—not in North America and certainly not overseas, where Maurer believes the frequency and quality of audits may not match the North American standard. The Zekelman team has found numerous instances of conduit manufactured outside of North America that bears a UL certification yet fails to meet UL standards.
The most common flaw they see? Inconsistent or insufficient metal coating to protect the conduit from corrosion.
“If you don’t have the right amount of corrosion protection, whether that’s zinc or an outer diameter coating over the zinc, then you could have premature corrosion in a system that would lead to a failure,” Maurer says.
That’s the sort of issue that might not be detected during installation, yet can lead to a failure just a few months or years later—dealing a subsequent hit to the electrical contractor’s reputation.
Put to the Test
Using premium, U.S.-made electrical conduit gives contractors peace of mind: It’s designed to install smoothly and built to last. And if there is a concern with product quality, Maurer says, “we’ll be on the job site tomorrow—not to point fingers, but to figure it out together.”
What makes American conduit manufacturing so consistent and reliable? At the Zekelman family of companies, it’s having a process built to deliver exceptional safety, quality, and performance every time.
- Testing: Various tests and procedures, such as humidity testing and salt spray corrosion testing, confirm that Zekelman products meet or exceed the UL standards.
- Quality checks: Zekelman team members pull steel conduit from the manufacturing line at regular intervals to check for weld integrity using a process called destructive testing—essentially, expanding the conduit on a cone until it gives out to ensure the welded joint meets or exceeds the target tolerances.
- High-quality materials and equipment: To ensure consistency in its coatings, Zekelman relies on a combination of premium materials and the latest factory equipment. That includes using premium zinc to coat the steel and incorporating modern technology into its galvanization processes: hot-dip galvanization for rigid steel conduit; in-line galvanization process for EMT and IMC; and electroplated couplings.
“We’ve taken the best technology across our organization, combined it with all of our years of experience, and put that together into those operations to try and be both as efficient as possible and also have the highest level of quality possible,” says Maurer.
High-end galvanization processes require major capital investments. Some low-cost foreign tube manufacturers forgo those in favor of less reliable approaches, such as buying pre-galvanized strips or steel coils, Maurer says. Going that route ultimately requires re-metallizing the weld seam—a common failure point with imported conduit that opens the door for quick corrosion failure.
Built to Last
For electrical contractors, the choice is clear: While imported steel conduit might slightly lower construction costs, it comes with substantial risks, including installation delays and increased chances of shorts and failures.
In contrast, high-quality domestic conduit provides dependable performance that contractors and their clients can trust.
“With domestic manufacturers, you’re going to get pride,” says Maurer. “You’re going to have the confidence that there are quality-assurance systems in place, and that those systems are constantly being audited both by internal resources and external third-party resources.”
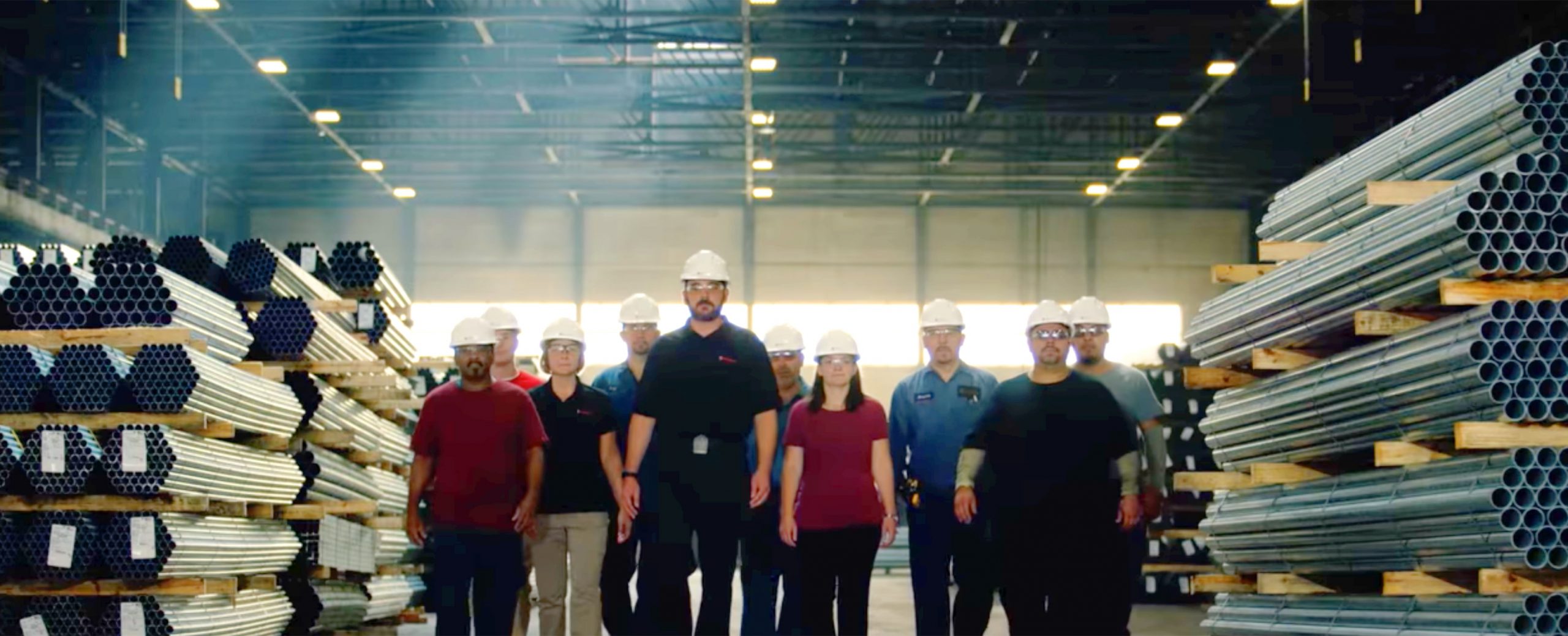
There’s nothing better than building something you believe in.
Zekelman companies are in constant motion, expanding our teams and challenging convention.
"*" indicates required fields